Automated Guided Vehicle AGV - The Smart Solution for Industrial Automation
Unlock the future of industrial automation with Automated Guided Vehicle AGV technology. Enhance efficiency, reduce costs, and improve safety in your warehouse or manufacturing facility.
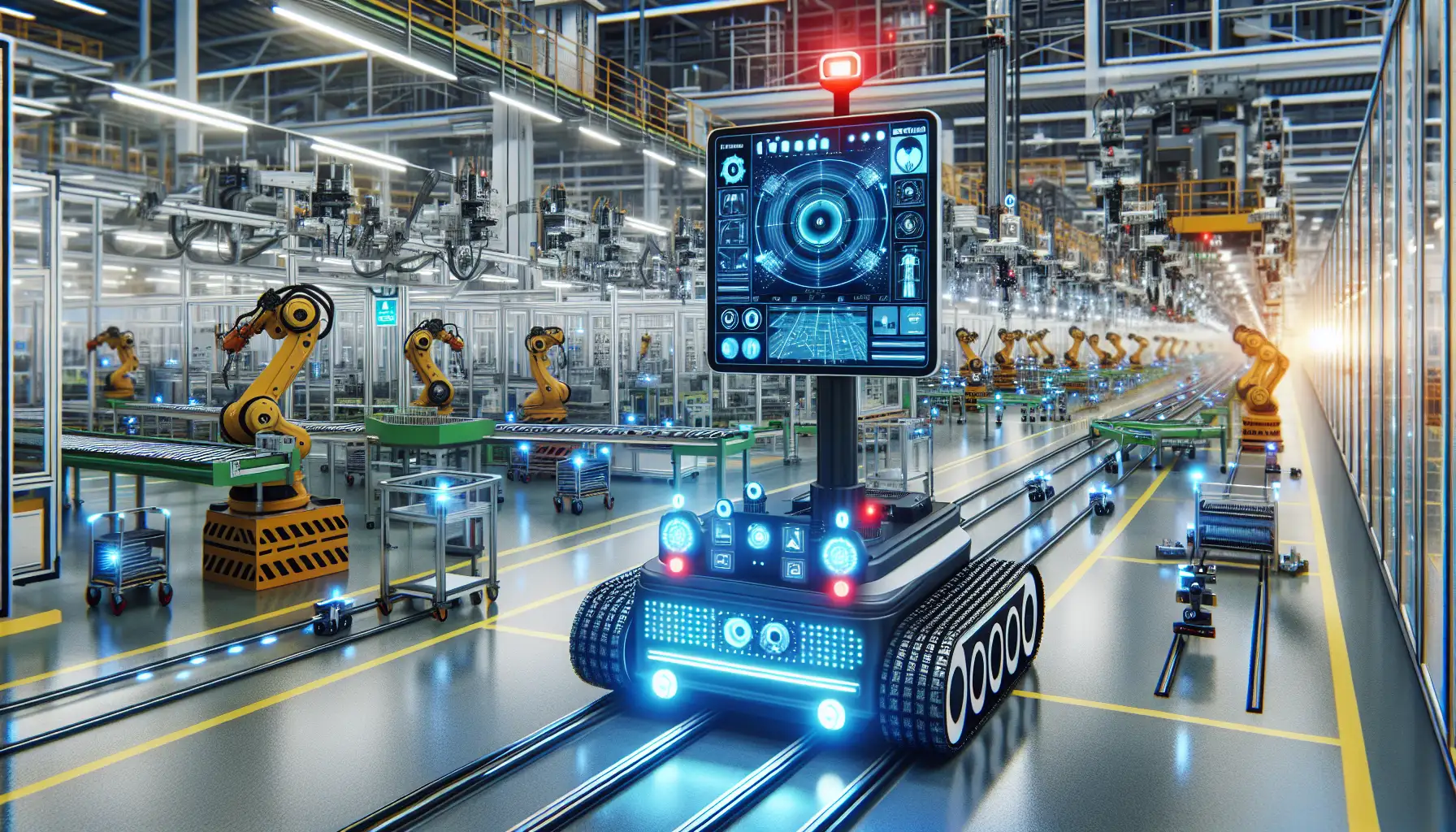
Warehouse Symphony: The Rise of the Automated Guided Vehicle AGV
Imagine stepping into a warehouse humming with the quiet efficiency of smart technology, where automated guided vehicles (AGVs) navigate seamlessly, orchestrating a symphony of logistics and manufacturing precision. As an IT engineer with over two decades of experience in the industrial automation landscape, I've witnessed firsthand the transformative power of automated guided vehicle agv in revolutionizing warehouse and manufacturing operations. This narrative isn't just about technology; it's about the future of industry, shaped by innovations that enhance human potential and redefine productivity.
In recent years, the adoption of automation has surged, driven by the need for increased efficiency, cost reduction, and improved safety. Automated guided vehicle agv, as part of this technological wave, play a pivotal role in modernizing our industrial processes. They are not just machines; they are the backbone of a smart, automated future. Let's dive into the world of automated guided vehicle agv and explore how they are changing the game in industrial automation.
Driving Efficiency: The Magic of Automated Guided Vehicle AGV
Defining AGVs
Automated Guided Vehicles (AGVs) are mobile robots used for material handling in warehouses, manufacturing facilities, and distribution centers. These intelligent machines are designed to follow predetermined paths or dynamically navigate their environment to transport goods efficiently. The core functionalities of automated guided vehicle agv include autonomous navigation, load handling, and real-time communication with central control systems.
Components of AGVs
At the heart of an automated guided vehicle agv are several critical components:
- Motors: Drive the vehicle and handle the loads.
- Sensors: Enable navigation and collision avoidance.
- Control Systems: Manage the automated guided vehicle agv's operations and communication.
- Batteries: Provide the necessary power for uninterrupted operation.
AGVs vs. AGCs
While AGVs and Automated Guided Carts (AGCs) share similarities, they are distinct in their applications and capabilities. AGCs typically follow fixed routes and are used for simpler tasks, whereas automated guided vehicle agv offer more advanced navigation and can handle complex material handling tasks.
Types of AGVs
Function-Based Categorization
Automated guided vehicle agv come in various types, each suited for specific functions:
- Unit Load Carriers: Designed to transport pallets or large containers. Commonly used in warehouses for bulk material handling.
- Towing Vehicles: Capable of pulling carts or trailers, often seen in manufacturing plants moving parts along the production line.
- Assembly Line AGVs: Used in automotive and electronics industries, these AGVs move components through assembly processes.
Load Capacity
Automated guided vehicle agv vary in load capacity, from small models handling a few hundred kilograms to heavy-duty versions capable of carrying several tons. This versatility allows them to be tailored to specific industrial needs.
Guidance Technology
Automated guided vehicle agv navigate using different technologies:
- Wired Guidance: Follow embedded wires in the floor.
- Magnetic Guidance: Use magnetic strips laid on the floor.
- Vision Systems: Employ cameras and sensors to interpret the environment and navigate autonomously.
Examples and Applications
In a large distribution center, unit load carriers efficiently move pallets between storage areas and shipping docks. Towing vehicles streamline the flow of raw materials in a manufacturing plant, reducing manual labor and increasing throughput. Assembly line automated guided vehicle agv enhance precision and reduce errors in complex assembly tasks, exemplifying their diverse applications.
Benefits of Using AGVs
Increased Efficiency and Productivity
Automated guided vehicle agv significantly boost operational efficiency by automating repetitive tasks and ensuring consistent performance. Studies show that implementing automated guided vehicle agv can increase productivity by up to 30%, as they operate without breaks and maintain a steady workflow.
Reduced Labor Costs
By automating material handling, automated guided vehicle agv reduce the need for manual labor, leading to substantial cost savings. This shift allows human workers to focus on higher-value tasks, fostering a more skilled workforce.
Improved Safety
Equipped with advanced sensors and collision avoidance systems, automated guided vehicle agv enhance workplace safety by minimizing accidents and injuries. The reduction in human error and the elimination of hazardous manual handling contribute to a safer working environment.
Enhanced Accuracy and Precision
Automated guided vehicle agv operate with a high degree of accuracy, ensuring precise placement and movement of goods. This precision minimizes errors and reduces waste, which is particularly beneficial in industries with stringent quality standards.
Increased Flexibility and Scalability
Automated guided vehicle agv offer unparalleled flexibility, adapting to changing operational needs and scaling up or down as required. This adaptability makes them ideal for dynamic industries where production volumes and processes frequently change.
24/7 Operation
Unlike human workers, automated guided vehicle agv can operate continuously, providing round-the-clock productivity. This capability is crucial for industries with high demand and tight deadlines, ensuring that operations run smoothly and efficiently.
Reduced Damage to Goods
The consistent and controlled movement of automated guided vehicle agv reduces the risk of damage to goods during transport. This reliability is especially important for delicate or high-value items, protecting them from the wear and tear associated with manual handling.
Quantifiable Benefits
According to industry benchmarks, businesses implementing automated guided vehicle agv report a 20-50% reduction in labor costs and a 10-30% increase in overall productivity. These figures underscore the tangible advantages of adopting automated guided vehicle agv technology in industrial settings.
Considerations for Implementing AGVs
Initial Investment Costs
Deploying automated guided vehicle agv requires a significant initial investment, covering the cost of the vehicles, infrastructure modifications, and integration with existing systems. However, the long-term savings and efficiency gains often justify this expenditure.
Facility Layout and Space Constraints
The layout of the facility plays a crucial role in automated guided vehicle agv implementation. Adequate space and well-defined pathways are essential for optimal automated guided vehicle agv performance. Evaluating and potentially redesigning the facility layout is a critical step in the deployment process.
Integration with Existing Systems
Automated guided vehicle agv must integrate seamlessly with existing warehouse management systems (WMS) and other automation technologies. This integration ensures smooth operations and maximizes the benefits of automation.
Maintenance Requirements
Regular maintenance is essential to keep automated guided vehicle agv operating at peak efficiency. Establishing a maintenance schedule and training staff to handle routine checks and repairs are important considerations for long-term success.
Return on Investment (ROI) Calculations
Calculating the ROI involves assessing the initial costs, ongoing operational savings, and productivity gains. Many businesses find that the ROI for automated guided vehicle agv is favorable, with payback periods ranging from one to three years, depending on the scale of implementation.
The Future of AGVs
Advancements in AGV Technology
The future of automated guided vehicle agv is promising, with continuous advancements enhancing their capabilities. Improved navigation systems and obstacle avoidance technologies are making automated guided vehicle agv more autonomous and reliable. The integration of artificial intelligence (AI) and machine learning (ML) is set to revolutionize automated guided vehicle agv, enabling them to learn from their environment and make real-time decisions.
Increased Autonomy and Decision-Making
Future automated guided vehicle agv will possess higher levels of autonomy, requiring minimal human intervention. These intelligent systems will be capable of optimizing their routes, adjusting to changes in real-time, and collaborating with other automated systems.
Potential Future Applications
Automated guided vehicle agv will find applications in a broader range of industries, from healthcare and pharmaceuticals to retail and e-commerce. Their ability to enhance efficiency, accuracy, and safety will drive their adoption across diverse sectors, transforming the way goods are handled and transported.
Conclusion
Automated guided vehicle agv represent a pivotal innovation in industrial automation, offering a blend of efficiency, safety, and adaptability. As the demand for automation continues to grow, automated guided vehicle agv will play an increasingly vital role in modern warehouses and manufacturing facilities. Their ability to operate around the clock, reduce costs, and improve accuracy makes them an indispensable asset in the quest for operational excellence.
FAQs
- What is an Automated Guided Vehicle (AGV)?
- An Automated Guided Vehicle (AGV) is a mobile robot used for material handling in warehouses, manufacturing facilities, and distribution centers. These intelligent machines navigate autonomously or follow predetermined paths to transport goods efficiently.
- What are the main benefits of using Automated Guided Vehicles (AGVs) in industrial settings?
- AGVs offer a range of benefits, including increased efficiency and productivity, reduced labor costs, improved safety through advanced sensors and collision avoidance systems, enhanced accuracy and precision in material handling, scalability to adapt to changing operational needs, 24/7 operation capability, and minimized damage to goods during transport.
- What are the different types of Automated Guided Vehicles (AGVs) available?
- AGVs can be categorized based on their function, load capacity, and guidance technology. Common types include unit load carriers for pallet transport, towing vehicles for material movement, and assembly line AGVs for assembly processes. They vary in load capacity, from small models handling a few hundred kilograms to heavy-duty versions capable of carrying several tons.
- What factors should be considered before implementing Automated Guided Vehicles (AGVs) in a facility?
- Several factors should be evaluated, including initial investment costs, facility layout and space constraints, integration with existing systems like warehouse management systems (WMS), maintenance requirements, and calculating the return on investment (ROI) based on cost savings and productivity gains.
- What does the future hold for Automated Guided Vehicles (AGVs)?
- The future of AGVs is promising, with advancements in technology leading to increased autonomy, improved navigation, and enhanced decision-making capabilities. AGVs are expected to find applications in a broader range of industries, further transforming material handling and transportation processes.